Since I just wrote about wood graining, I thought it would be appropriate to share this passage written by Nathaniel Whittock back in 1828 on the subject:
It is of great consequence in imitating oak that the joiner’s work should be represented naturally as well as the wood. The practitioner in graining who resides in any large town, will have ample opportunities in observing the work of others, and improving from their beauties, and even from their defects. If a new oak door is to be formed, the joiner is solicitous to select wood as finely flowered and free from knots as it can be procured; and if a join is made in a panel he is anxious that the wood should be of the same colour, and if possible that the grain and flower should match, as nothing would look worse in his eye than knotty wood and difference of colour.
And yet it is the constant practice of the painter, in order to shew his skill in graining, to make both those faults show as glaringly as possible. Nothing can be more offensive to the eye of taste than to see the panels of a door joined at all; but if the painter chooses to shew his skill, let the joint appear neatly put together, and shew the joint by combing the grain in opposite directions. The common error is to form the joint by glazing part of the panel with a glaze of vandyke brown, leaving the other part the natural color of newly cut oak. This certainly shews a joint, but shews it much in the same way that a tailor would shew his skill in patching a hole in a black coat with a piece of scarlet cloth.
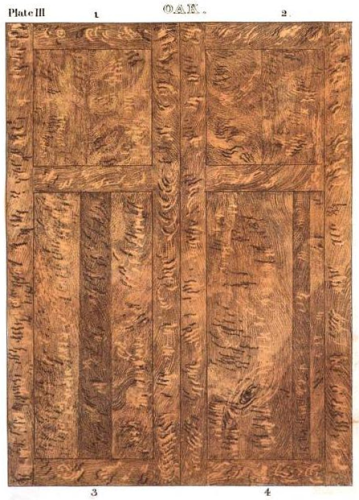
Editor’s note: The word “shew” used here is simply an older spelling variation for the word “show”. Originally published in The Decorative Painters’ and Glaziers’ Guide, by Nathaniel Whittock. London: Isaac Taylor Hinton, 1828, pp 24-25.