The following comes from “The Illustrated Magazine of Art”, Volume 4, Number 24, page 344, published in 1854. I thought the process they described was interesting. First, it is the first time I’ve heard of using metal molds for papier maché; second, they let each layer dry fully before applying the next (I learned to lay up each layer while the previous is still damp).
The polished French claim the honour of being the original inventors of the papier maché. In Paris the manufacture of the article is carried on very extensively; but far beyond the articles produced there—articles both of utility and ornament—stand those of the Birmingham manufacturers.
The old method of manufacturing papier maché is as follows:
—The paper for use is gray in colour, but similar in texture to ordinary blotting paper. Prior to using it, the paper is well saturated with flour and glue mixed with water, in about equal proportions, and is then laid on the mould of the article intended to be produced. These moulds are of iron, brass, or copper. The mould, coated with the first layer of paper, is then dried for twelve hours. A careful smoothing by a file follows, after which another deposit of paper is made. The processes of drying and smoothing are successively repeated with each additional layer of paper, until the article assumes the required strength and thickness. When the newly-formed article is taken from the mould, the several parts are planed, filed, and trimmed, so as to be quite correct and level. The process of stoving then follows; after which the varnish is laid on, and brought to a smooth, hard, brilliant surface. The article is then coated with several layers of shell-lac varnish, coloured, which, after being hardened, are scraped quite level. The different varnishings and smoothings are carried on for a period varying from twelve to eighteen days, according to the purpose for which the article is required. The exquisite surface is produced by manual polishing with rotten stone and oil; but the finish is obtained by the process of handling alone.
Various alterations and improvements have been made from time to time in the manufacture of papier maché; and sometimes the paper is reduced to pulp, cast to the form required, and then rendered compact and solid.
The specimen which we present is of a chair in papier maché; the grace and elegance of the design deserve especial attention.
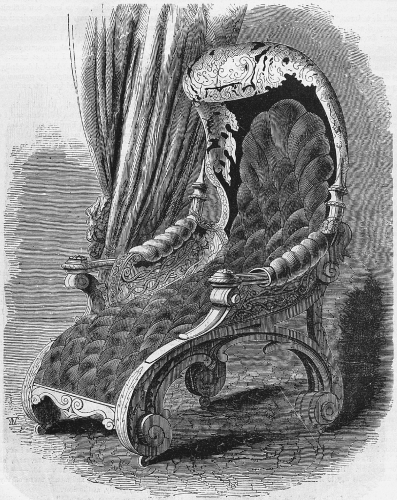
Papier Mache Chair. The Illustrated Magazine of Art, Vol. 4, No. 24 (1854), p. 344