Our last show of the season at Triad Stage is All’s Well That Ends Well, a Shakespeare piece I had worked on before (you may recognize the cannon I built for the previous production at Shakespeare in the Park). There were no cannons this time around, but we did need a crown for the King of France. Since Shakespeare isn’t our typical shtick, we did not have any crowns in stock. I had to make one.
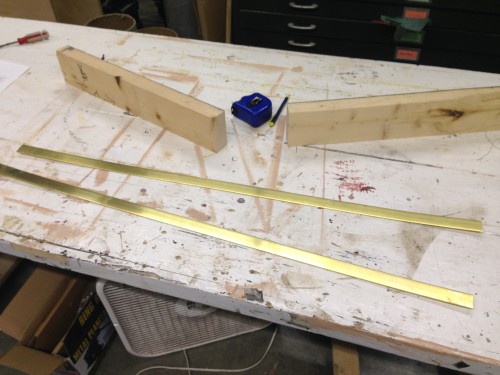
The base of the crown was a piece of one-inch wide brass bar that was 3/16″ thick. I ordered a long piece of it from McMaster Carr in case I messed up and had to make another one.
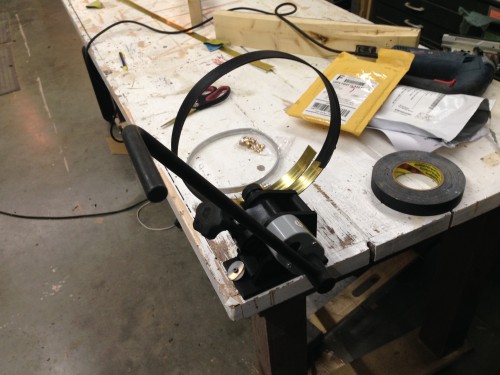
I ran it through a cheap little ring bender from Harbor Freight. It’s small, but it can handle metal up to an inch wide, so I was golden. I covered the brass bar in tape because the wheels on the bender marred up the soft metal. The bender made a nice circle, but since the crown was actually an oval, I had to do some shaping by hand to get it just right.
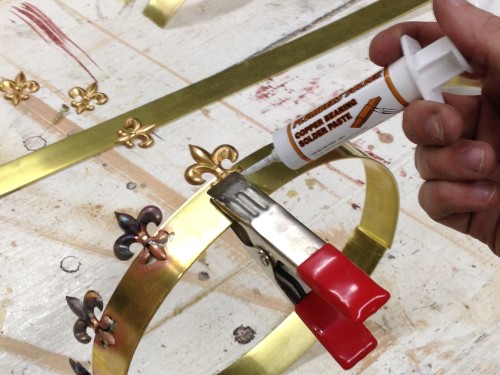
I had some stamped brass fleurs-de-lis which I needed to solder on. I discovered “solder paste”, which is a mixture of flux and powdered solder in a liquid form. You just squirt it into the joints you want to be soldered and then run a torch over it until it melts.
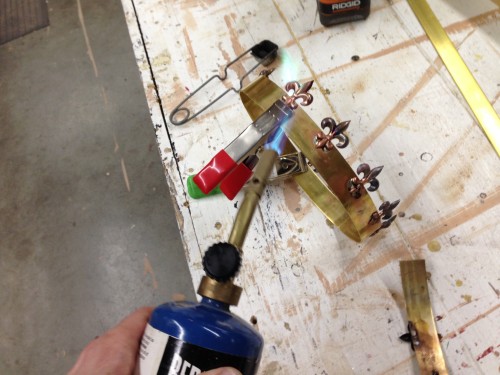
Since the solder paste has a very low melting temperature, I could use a regular propane torch from any hardware store. Brass has a very low melting temperature, and since the fleurs-de-lis were very thin, I was worried that any kind of brazing or silver soldering would melt them before it melted the solder. The solder paste was a great solution.
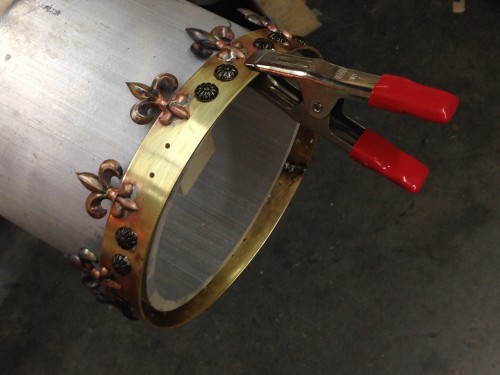
Next I added some decorative upholstery tacks to the crown. I drilled some holes for the tack part to stick through. At first, I thought I could solder them on from the back, kind of like plug welding. That wasn’t working, so I just soldered them from the front. I was using this giant piece of aluminum tube as a heat sink so that the torch would not de-solder the pieces I had already soldered.
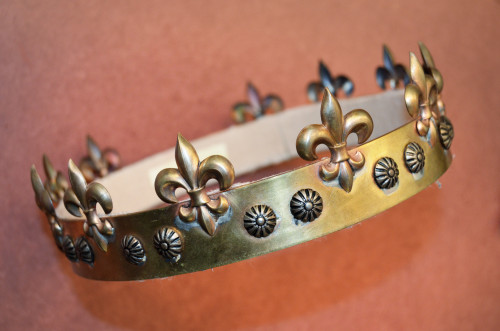
I was able to remove all of the charring and discoloration with some #000 steel wool. I lined the inside of the crown with moleskin, a very thin but soft padding. You can find self-adhesive pads of it in any drugstore near the foot pads and shoe inserts.
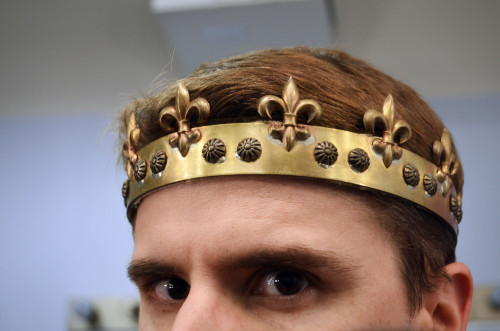
I think you can get the solder paste in a copper or brass color; I was going to cover up all the silver bits of solder with some brass craft paint, but they didn’t show up once the crown was on stage. I think I look pretty good as a king.