From 1995 to around 2004, a magazine known as Proptology was published by a Canadian props professional named Wulf. He published a multi-part series called “A Field Guide to Furniture Styles”, which contained a lot of useful illustrations and information for identifying period Western furniture. One of the parts had a nice little list of chair backs. I have taken this information and these illustrations and arranged them in a nice little grid where they are grouped by similar appearances.
I have some other helpful illustrations in previous posts: analysis of a chair, 40 styles of chairs, and parts of a chair. Armed with these images, we are well on our way to developing a visual guide to identifying the period of a chair based on its appearance.
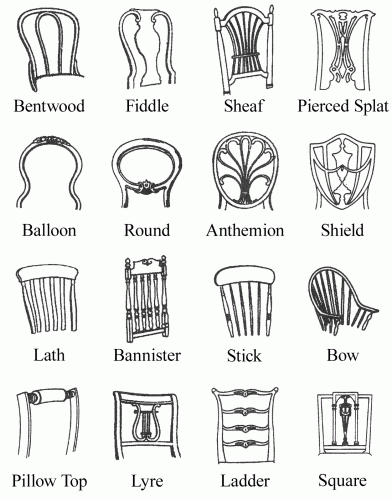
Bentwood: Late 1800s.
Fiddle: Characteristic of Queen Anne style. 1700s.
Sheaf: Can also be a splat which is pierced in the same style. Late 1700s.
Pierced Splat: Characteristic of Chippendale designs. Late 1700s.
Balloon: Characteristic of Victorian style. Mid 1800s.
Round: Often an open frame with no upholstery. Mid 1800s.
Anthemion: Greek motif favored by Hepplewhite. Late 1700s.
Shield: Characteristic of Hepplewhite. Late 1700s.
Lath: Curved, flat uprights. Very sturdy. 1800-1900s.
Bannister: Like stick back but with turned posts. 1600-1800s.
Stick: Primarily used in country furniture. 1600-1800s.
Bow: Typical form of Windsor style chair. 1600-1800s.
Pillow Top: A narrower top is called “Bolster Top”. 1800s.
Lyre: Popular motif in Empire style designs. Early 1800s.
Ladder: With pierced splats is called “Pretzel Back”. 1400-1900s.
Square: Characteristic of Sheraton’s designs. Late 1700s.