With this summer’s season at the Santa Fe Opera at an end, I can begin to show off some of the props I’ve built there. First up is a giant champagne bottle.
We needed four champagne bottles of a very specific size; they were going to be the barrels of cannons that I would also build. Nobody manufactures champagne bottles that large, so we had to make them. Since we would vacuum-form them from plastic, I began by making a solid foam bottle.
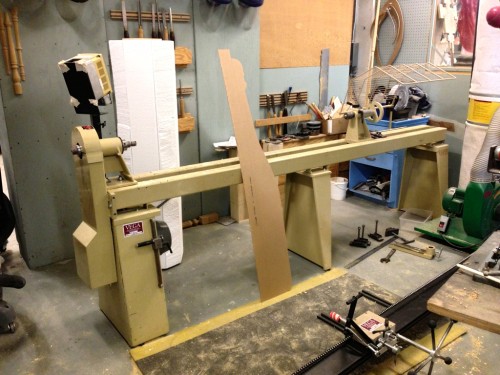
I drew out half the shape at full-scale on a piece of plexiglass. We have a duplicator on our lathe, which allows us to rough out the shape by directly following a pattern like this. I also got the block of foam ready. This piece was so wide, it barely fit on the lathe; I had to take most of the attachments off and round off the foam by hand before there was enough room to put the attachments back on.
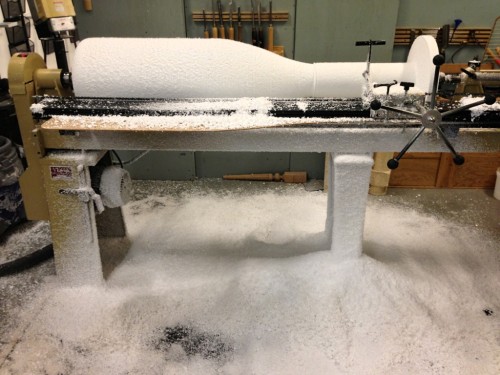
As you can imagine, turning a block of foam this large creates quite a bit of debris. I am still finding bits of foam in my clothes to this day.
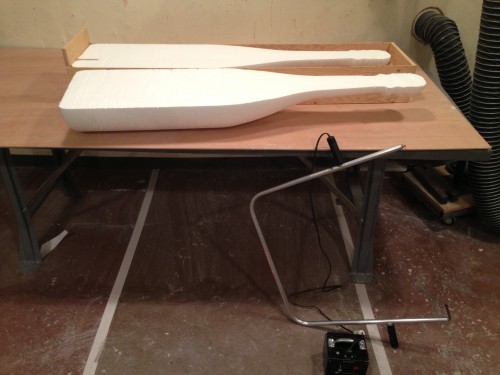
To vacuum form this piece, I only needed half of the bottle. I built a box so I could hold the bottle straight. The top of the box reached the exact middle point of the bottle, so when I ran a hot wire along it, it sliced the foam bottle directly in half.
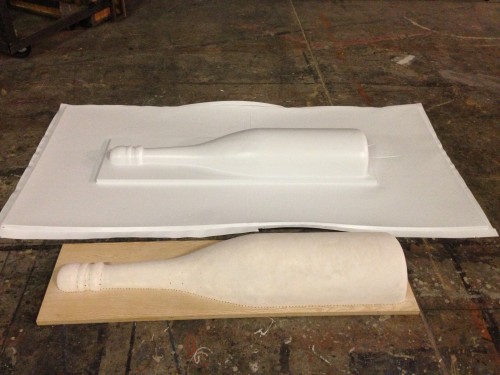
I mounted the foam onto a board and drilled holes all around the circumference, as well as holes in the concave portions to ensure the plastic would be sucked all the way down. I also coated the foam with Aqua Resin and sanded it smooth. I posted a video a few weeks ago showing the vacuum forming machine in action; check it out if you want to see how I made the piece in the photo above.
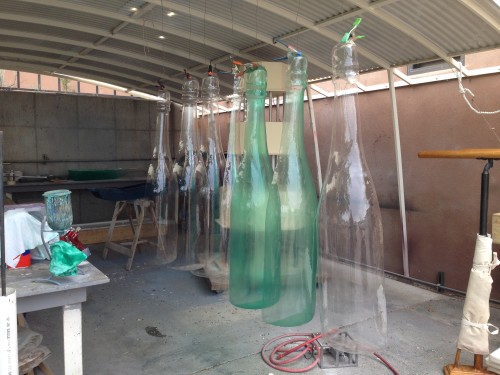
With a successful pull on the vacuum former, this project was turned over to the crafting department, and my work on it ended. They began manufacturing clear plastic halves like you see above, and spraying them down with green dye to match the color of a real champagne bottle.
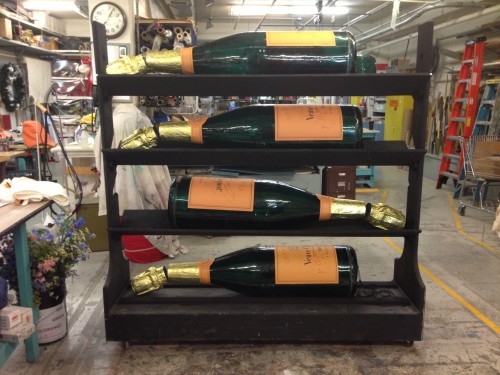
They glued the halves together and added some labels and gold foil to complete the look. The final bottles were over four feet tall.