A few weeks ago, I built myself a new coffee table. It’s not a prop, but I thought I’d show some pictures anyway. We had a set of IKEA shelves in last fall’s production of In the Wake; one of the shelves was just the right size for the top of the coffee table. I gathered the rest of the materials from scraps of lumber that had been sitting around the prop shop for a long time. I kept the design simple; it was almost like a modified trestle table, with a single center stretcher, and the legs had a slight angle to them.
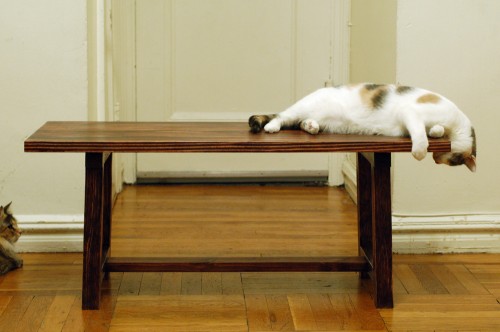
All the wood I used was pine. While I like the grain pattern of pine, I can’t really stand light-colored wood, so I applied a coat of red mahogany stain to it. One of the things I rarely get to do when making props is put a nice finish to a carpentry project; usually we just slap a coat of polyurethane on and call it done. I decided to go with two coats of shellac. The denatured alcohol means it has some VOCs when you are working with it, but when that is fully evaporated, you are left with just the resin from the lac beetle, giving you a natural finish which is both food-safe and hypoallergenic. You can build up a really nice and hard finish by applying several thin coats with sanding in between. One of the other things that makes it great is that each coat dries in about an hour, as opposed to the 24 hours it takes for a coat of Tung Oil to dry. I applied one coat, sanded it with 220 grit sandpaper, added a second coat, and sanded that with 400 grit paper. The finish protects the stain from coming off the wood and moisture from going into the wood. It leaves the wood slick and smooth without really obscuring its natural appearance (or making it look like a shiny piece of plastic like some horrific finishes you see).
Because I built this in the prop shop, I needed to bring it home when I was all finished. Being in New York City without a car means I had to bring it on the subway. With that in mind, I had built it so it could be broken down into four pieces which just needed to be screwed together. Basically, I had made my own “flat-pack” furniture. I shrink-wrapped the pieces up and carried it home with ease.
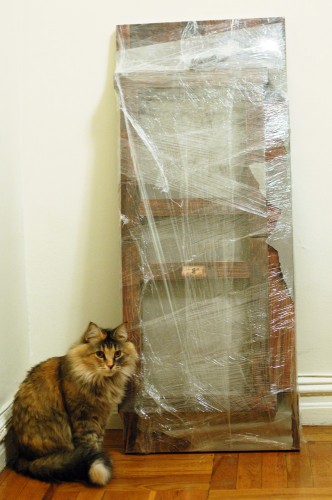
I even labeled the joints so I knew which way the pieces went when it came time to reassemble it.
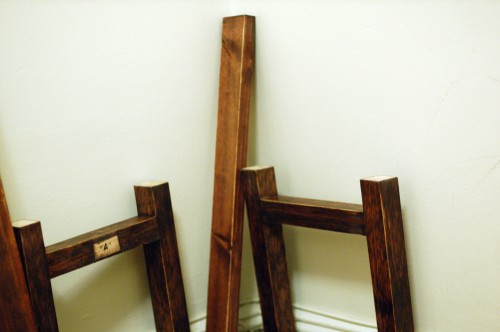
Obviously, my cats were very interested in this new arrival. Biscuit especially seemed to approve of it.
